「3Dプリンター設備+専門家の知見」の総合支援で生まれた、かつてない構造のスピーカー
公開日:2021年6月15日 最終更新日:2024年11月8日
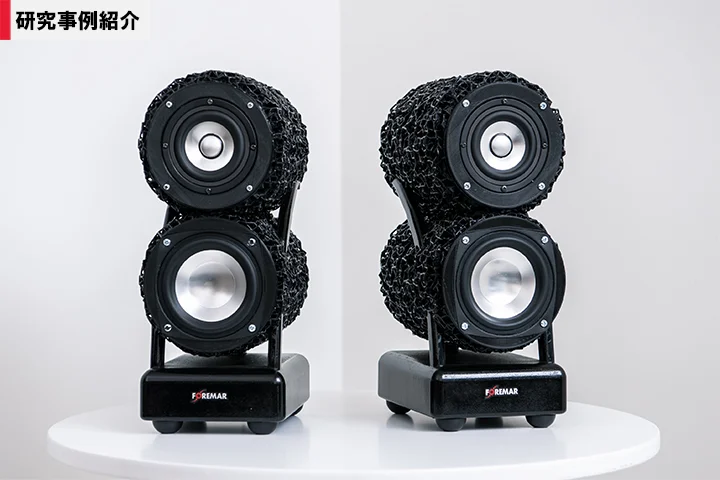
都産技研はフォレマー合同会社が開発した開放吸収拡散型スピーカー「FOREMAR FRM」について、設計・試作などの上流工程の支援および、性能向上を目的とした共同研究を行いました。
「FOREMAR FRM 30」(以下FRM 30)は、これまでのスピーカーとは異なる特殊な構造をしており、3Dプリンターによって成形を実現しています。FRM 30は製品化に至るまでどのような道のりをたどったのか、フォレマー合同会社 代表社員の植木 準 氏と、製品化技術グループの山内 友貴 主任研究員に話を聞きました。
3Dプリンターでしかつくれない「理想のスピーカー」
フォレマー合同会社は、独自の高音質音響機器を開発するオーディオデザインの会社として、2018年に設立されました。FRM30のアイデアは、オーディオマニアでもある植木氏が「理想のスピーカー」として会社設立前から温めていたといいます。
「一般的なスピーカーは、スピーカーユニット内のコーン紙を振動させて、前面に音を出します。ただ、コーン紙が“面”で振動している以上、背面にも逆位相の音が同じ音量で出ているのです。背面に出た音は、スピーカーの箱の中に閉じ込められますが、反射による漏れや、振動による箱鳴りがどうしても雑音となってしまいます」(植木氏)
原音に忠実な音を再現するために、植木氏は無数の細かい枝が複雑に絡み合った「非結晶構造体」によるスピーカーを考案しました。
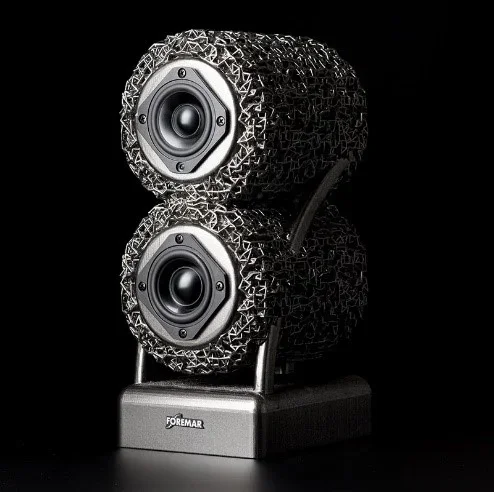
それぞれの枝の太さや長さは一定ではなく、枝に当たった音を拡散させる効果がある。
コーン紙の背面から出た音は、本体を包む細かい枝の一つに当たり、減退とともに拡散します。拡散した音はさらに別の枝に当たり、またさらに……と、繰り返すことで、雑音となる逆位相の音が吸収されるしくみです。「防波堤の消波ブロックと同じ原理」と、植木氏は説明します。
「この構造はあまりにも複雑なので、型で成形することができません。3Dプリンターが登場したことで、思い描いた形のスピーカーがつくれると考えたのですが、最初は思ったような試作品ができませんでした。3Dデータをつくって出力してみると、どうしても歪んでしまうんです。そこで、より理想の形状に近づけるため、都産技研に相談することにしました」(植木氏)
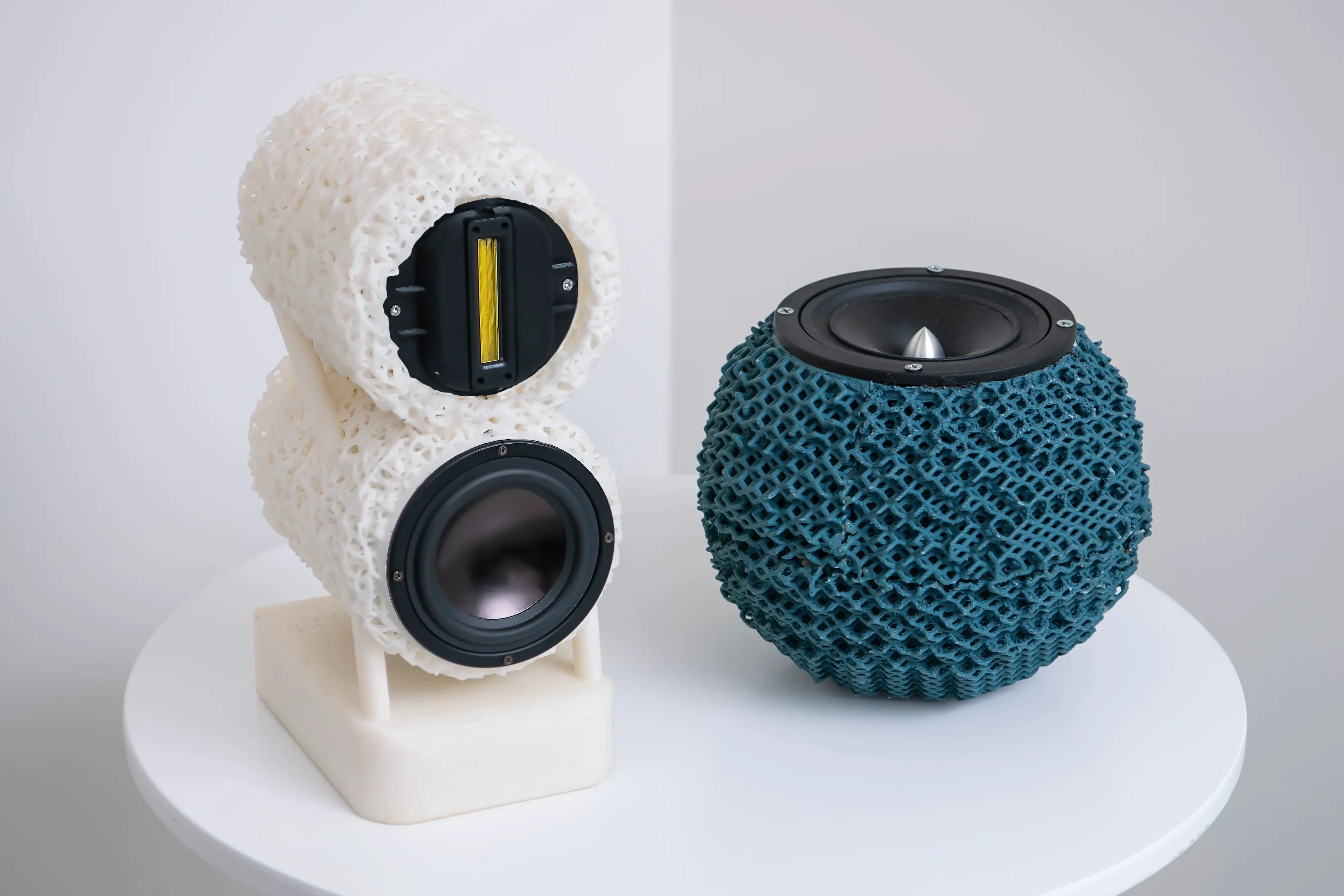
一体成形ができなかったため、構造を8分割し、パーツを接着剤で貼り合わせている。
材料や造形方式の選定を行い、試作品の出力を支援
技術相談を受けた製品化技術グループの山内研究員は、構造体を出力する際の造形方式に着目しました。
「最初の試作品は“材料押出方式(MEX)”の3Dプリンターでつくられていました。溶かした材料を積み上げるシンプルな造形方式なのですが、下から積み上げるため、溶かした材料の下に支えるものがないと垂れてしまいます。そのため構造体が歪んでしまったと考え、別の“粉末床溶融結合方式(PBF)”の3Dプリンターを薦めました」(山内)
粉末床溶融結合方式は、素材となる樹脂粉末にレーザーを照射し、溶融結合する造形方式です。樹脂粉末の中に造形物ができるため、常に支えとなるものがあり、複雑な形状にも適しています。
「最終的に樹脂粉末の中から造形物を取り出すため、構造体の中に粉が残らないように設計する必要がありました。そこで枝の密度や太さといったパラメータをすり合わせ、製品化技術グループの設備で試作を行いました」(山内)
試作では、強度や劣化を踏まえた材料の選定、3Dデータ作成時のエラー対処など、多くのアドバイスをいただきました。私自身、ものづくりについては全く経験がなく、『3Dプリンターは思ったものがなんでも形になる』とすら考えていたので、今回の支援は本当に助かりましたね」(植木氏)
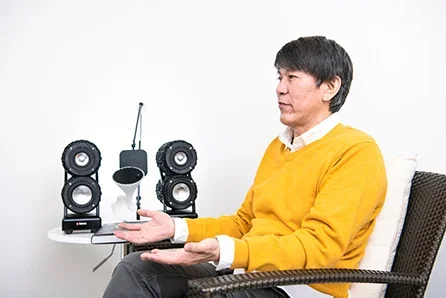
最初の相談から1年あまり、ようやく理想とする構造体が一体成形で完成しました。実際にスピーカーユニットから実際に音を出し、音質が向上したことはわかりましたが、植木氏には「さらに理想の形に近づけたい」という思いがありました。そこで、2020年度には製品性能の向上を目的とした共同研究が行われました。
「3Dプリンター+α」の総合的な支援で、ものづくりに貢献する
共同研究は製品性能を定量的に評価することを目的とし、評価手法を検討することから始めました。
しかしコロナ禍となり、実際に共同研究に着手できたのは7月のこと。構造体の枝の太さや密度、厚さといった要素を整理し、主要なパラメータを組み合わせた試作品で評価することにしましたが、全ての組み合わせを出力するには期間にも予算にも限りがありました。
「構造が複雑なだけに、出力には1回につき5日から1週間程度かかります。そこで、構造体のサイズを評価できるギリギリまで小さくし、3Dプリンター内で一度に複数の造形物をつくれるようデータを調整することにしました」(山内)
パラメータを変えた3Dデータを用意するのも簡単ではなく、実際に造形がスタートしたのは11月の終わりごろ。10パターン以上あるパラメータの組み合わせから5、6パターンに絞り、スピーカーを組み込んだ評価が行われました。
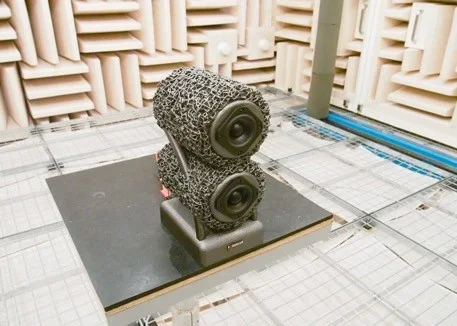
定量的な評価が行われた。
「評価には、都産技研に所属する音や振動のスペシャリストにも加わってもらいました。音響特性や筐体の振動などを計測し、総合的な判断でベストな構造を決めています」(山内)
「“いい音”の基準が人によって異なるのが、オーディオ評価の難しいところです。高音が持ち上がれば良い音だ、と感じる人もいれば、低音が響けば良い音だと感じる人もいる。今回は音質そのものの評価は行わず、最終的に “誰が聞いても違いがわかるか”という観点で判断しました」(植木氏)
こうして完成したFRM30は、プロ向けのスピーカーとして製品化され、現在は受注生産で販売されています。今後の展開について植木氏は「量産も視野に入れたい」と話します。
「現在は台座まで全て3Dプリンターで一体成形をしており、工業製品としてはさらなる考慮の余地があります。今後、量産に適した形状やデザインなどを検討したく、引き続き都産技研さんにご相談できればと思います」(植木氏)
「3Dプリンターは“試作品をつくるもの”というイメージがありますが、近年は造形技術の進歩から、製品製造に用いる動きも出てきています。3Dプリンターでしかつくれない構造のFRM30は、まさにその事例としてふさわしいのではないでしょうか。都産技研は3Dプリンターなどの設備に加え、さまざまな専門家が知見を提供できるのがなによりの強みです。こうした総合的な支援により、今後も皆さまのものづくりに貢献できればと思います」(山内)
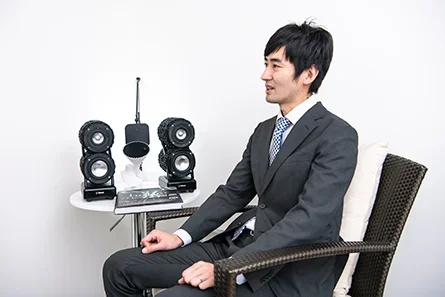
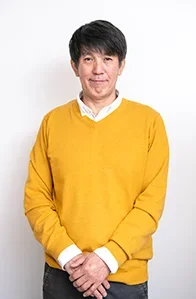
フォレマー合同会社
植木 準(うえき じゅん)氏
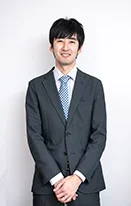
事業化支援本部 技術開発支援部
製品化支援グループ
主任研究員
山内 友貴(やまうち ゆうき)
関連情報
- フォレマー合同会社(外部リンク)
- FOREMAR FRM30(外部リンク)
- 製品化技術グループ
- ナイロン粉末造形装置
同じカテゴリの記事